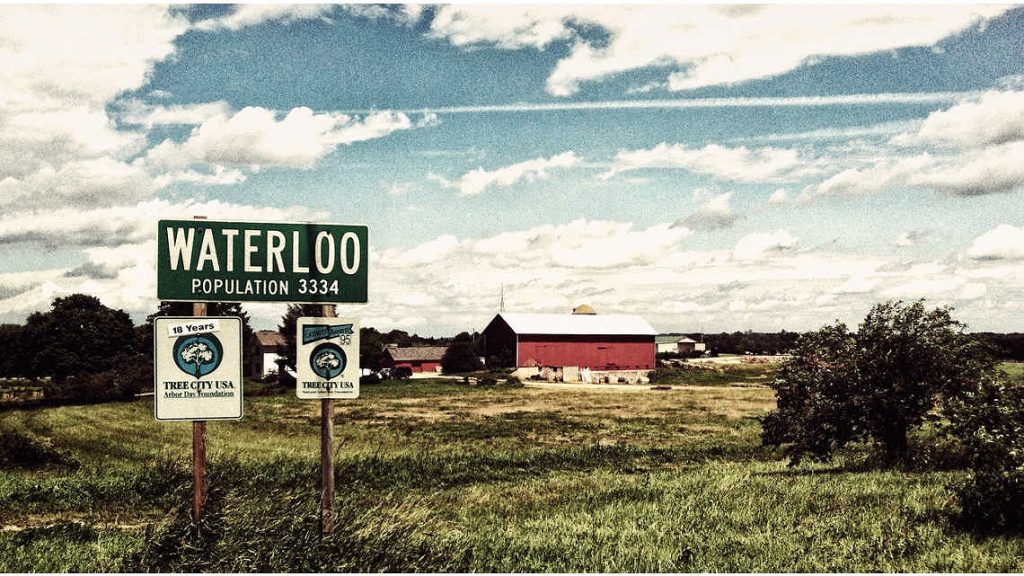
はじまり
トレックは、1976年にウィスコンシン州南部にある小さな赤い倉庫で、「世界一のバイクづくり」を夢みた二人の仲間により始まった。
そこには、すべてのバイクを誇りと共につくり上げるという、真なる職人文化が根付いていた。このルーツからずいぶん遠くまで成長した今も、我々の作るすべてのバイクは創業時のビジョンを具現化している。
Trek History
SENGA CYCLEの考える、バイク・ブランドとしてのTREK
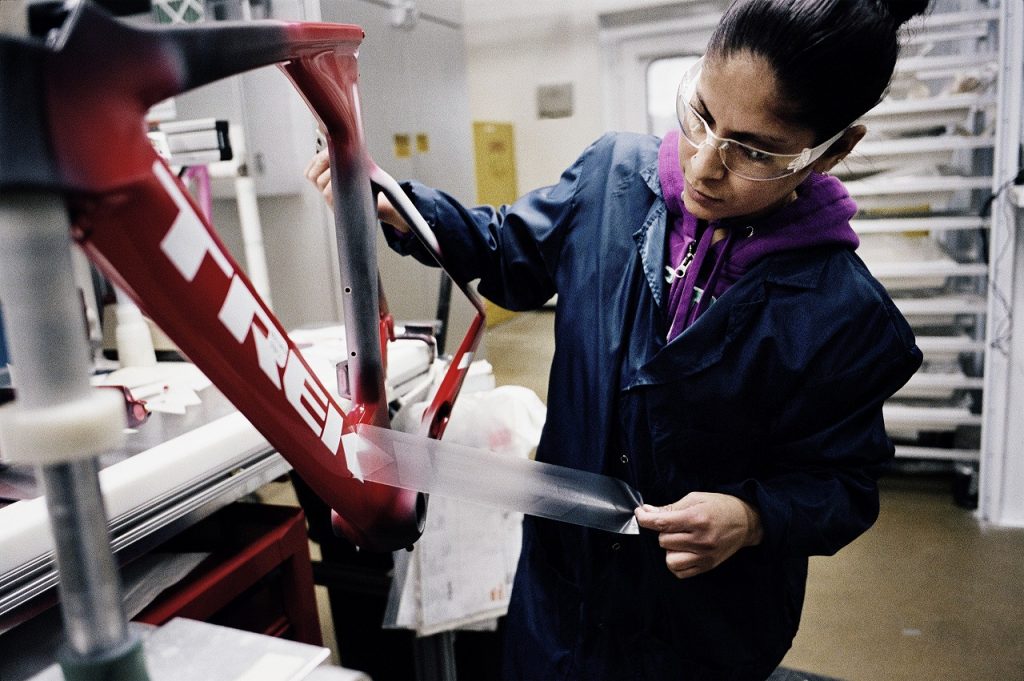
競技車両としての確かな実績
健全経営に裏打ちされた豊富な資金力と開発力
(株式未公開による安定経営・NASAにも劣らない最先端カーボン技術・最先端素材の利用方法の研究)
飽くなき職人魂で築かれる技術力
(厳密なバイクフレームとしての生産管理)
そして何より創業から変わらないものがあります。それは、、、
世界のユーザー(お客様)すべてがファミリーである
というぶれない企業理念!
これらの考えに基づき、
業界でいち早く「限定生涯保証」制度の採用
購入後の破損にもできるだけ安心を 「ロイヤリティ・プログラム」
他の追従を許さない、NASAにも負けないカーボン技術
健全経営だからできる、完全自社による最新素材の研究開発コスト
ビッグネームだからできる、他社(シマノ、FOX、ヘクセルなど)との提携共同開発
など、
お客様に確かな品質と安心
を届け続けてくれています。
これらを総合判断して、現在はTREKをメインにおすすめしています。
ロケットサイエンスによる技術革新
秀逸なパフォーマンスへの道には、好奇心が敷き詰められている。
1976年、トレックはある疑問を基に設立された:アメリカ国内でバイクが製造されていないのはなぜか?
今日、トレックは最も賢く情熱的なサイクリングデザイナーと研究者にあらゆる課題を投げかけている。
難しい質問に立ち向かい、まだ見ぬ境地へ行こうとするときにのみ、発明が生まれるからである。先頭に立つためには、開発投資は必須だ。
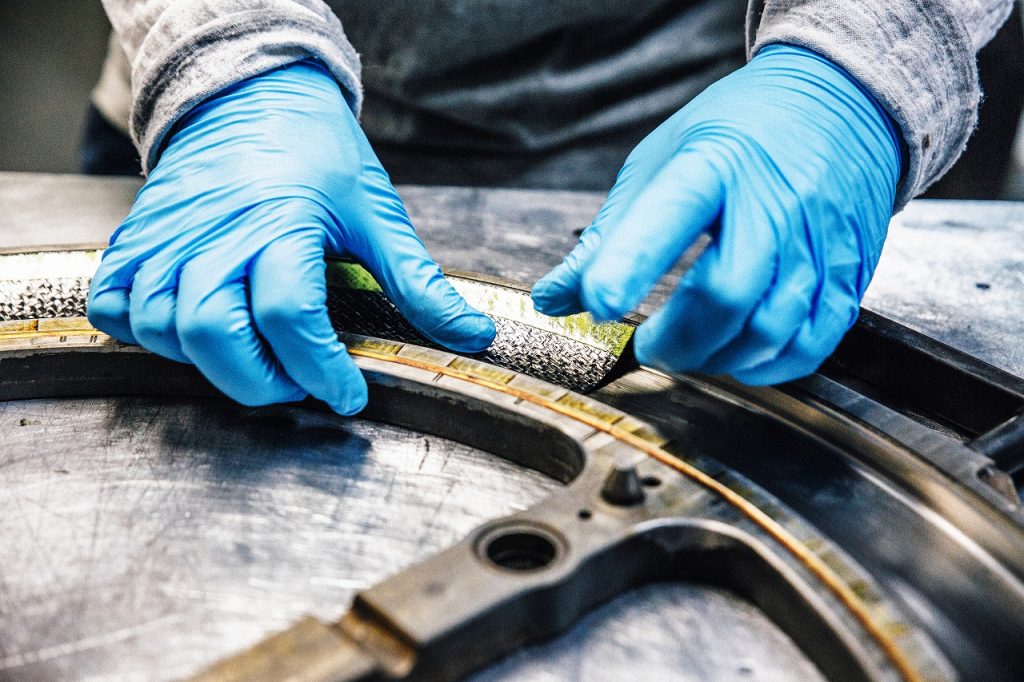
OCLV カーボン
Optimum Compaction Low Void の略。
巧みに作られたカーボンフレームは、金属製フレームと比べて大幅に軽くなりながらも、高い性能とライダーが求める強度と剛性も備えている。
ここで、先駆者であるトレックの特許取得済みのOCLVカーボン--Optimum Compaction Low Void(超高密度圧縮、低空隙)--製法が輝く。
OCLVカーボン製法は、最高の素材から始まる。
アメリカ国外には輸出禁止となっている軍事レベルのカーボン素材を基に、トレックは数えきれないほどの研究時間をつぎ込み、カーボンの編み方(クロスか、ユニディレクショナルか、など)、重量などカーボンの特性を調べつくした。OCLV製造方法は、2つに分けて説明するとわかりやすい。
Optimum Compaction
超高密度圧縮
カーボンは、繊維とレジンとが理想的な割合となるよう、いくつかの層に分けて配置され、重ねられる。
プリプレグと呼ばれる大きなカーボンシートを特殊な形状へ切り取り、鋳型に適切に配置するところからスタートする。
熱と圧力とを交えつつ、複数のカーボンシートをカーボンラグに圧着させていく。
この熱と圧力との組み合わせが、OCLVの基本となり、均一性を保つ重大なカギとなる。
Low Void
低空隙
空隙とは、コンポーネントやフレームを構成するカーボンファイバーの層間に存在する空間のことである。
これら空隙を最小限に抑えることが、高品質のカーボン製作で最重要のゴールなのだ。
空隙が増えると、このコンポジット素材の強度と耐久性が下がるからである。
OCLVカーボンは、空隙の含有率に関して、航空宇宙産業の水準を満たしている。
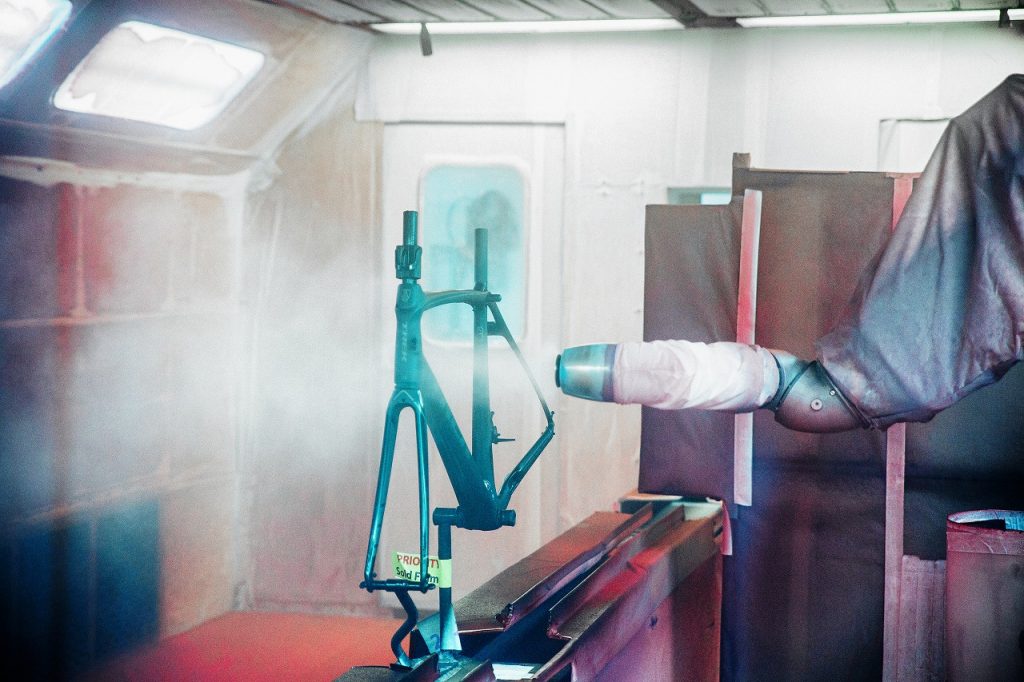
形状が非常に重要
重量をそぎ落とす上で、カーボン繊維が他の素材より優れる最大の点は、鋳型に合わせて素材の形状を自由に変化できることだ。
異なる形状とは、異なる強度を、そして空力数値に影響を及ぼす。
トレックは、シミュレーションツールソフトを用いたFEA(有限解析法)にて、形状の違いがライダーや走行路面にどのような反応を示すかを調べた。
さらにはCFD(コンピュータを用いた数値流体力学)も用いて、様々なデザインの空力性能特性の調査を行った。
私たちの作るバイクは、コンピュータによる計算が生んだデザインや流体力学を基に設計され、その結果として生まれた形状を機械がシームレスに具現化している。
最終的にこの複雑な科学的調査は、現場で一から複数の型を様々なカーボン素材と組み合わせる製法に適用され、徹底的に設計され、大部分がハンドメイドで作られる製品になる。